
LiFeTech
lithium iron phosphate battery
kimberley
kamper install
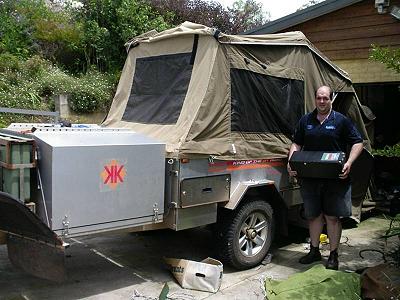
Ben Lace with the
12volt 180Ah lithium iron phosphate
battery
The aim of this article is to explain the steps taken in installing
a LiFeTech lithium battery in a Kimberley Kamper camper trailer to
replace the original manufacturer supplied lead acid batteries. Ben
Lace, the owner of a Kimberley Kamper decided after much research to
contact Lithium Batteries Australia with a view to upgrade the
battery system in his camper to lithium. I personally provided
assistance with the installation of the battery at Ben’s home as
well as the training of the battery diagnostics system.
So one warm summer Sunday
recently I spent the day with Ben installing his battery, charger
and battery monitor. We hope this step by step article will be
helpful to those camper trailer owners who are contemplating
upgrading their battery to lithium so as to have a much more
efficient and lighter weight battery system and which provides far
superior performance compared to any lead acid battery.
modifying
the battery tray
The factory supplied
batteries were six 35Ah Exide sealed lead acid batteries. These fit
end to end in the metal carrier which is located under the bed. It
was found that the most suitable lithium replacement battery was a
single 12V 180Ah lithium iron phosphate (LiFePO4) battery from the
LiFeTech Energy HPS series. This battery was found to be the perfect
height and allowed approximately 20mm of air gap between the top of
the battery and the bottom of the bed. Ben was able to make a slight
modification to the tray to hold the lithium battery by welding a
narrow frame to prevent the new lithium battery from sliding. It was
found that the lithium battery length was only half of the length of
the battery tray and a second battery could be fitted in the
remaining tray length available. Ben remarked that in future he
could further modify the battery tray so as to fit a second,
identical lithium battery should he decide to add air conditioning
to his camper at a later date.
installation of
battery, charger, battery monitor and battery/computer data box
Due to inaccessibility of
the batteries under the bed the LiFeTech batteries are the best
“drop in replacement” for the old lead acid batteries since they
feature inbuilt battery management system (BMS) and a low voltage
cut off protection board. In addition to the power connections for
12V at the battery terminals, a data type connector plugs in to the
DB9 data port fitted to the front of the battery between the
positive and negative battery terminal posts. This data cable was
run under the bed and down along the side of the camper to the
entrance of the van. Close to the entrance door of the camper was
decided by Ben to be a convenient location for plugging in his lap
top computer via the supplied battery data converter box and
software for detail checking of his battery without having to go to
the trouble of removing his bed again to gain access to the battery
in the far front corner.
With the bed entirely
removed it was simply a matter of refitting the modified battery
tray and fitting the new lithium battery and wiring. The original
lead acid batteries are all connected to each other with six pairs
of battery connection terminals this was no longer needed since
connection was now only required to be made to a single battery.
Therefore only one pair of lugs was crimped to the main power cable
leading from the battery to the load/output supply power wiring
providing power to the LED lights, fridge and other electrical
appliances being supplied by battery power. An additional heavier
gauge cable was also connected to the battery cables and run a few
metres to the location near the door where the data connector was
located. An Anderson connector was fitted to this cable to allow the
high power lithium battery charger to be plugged into this point.
All the cables were neatly cable tied in position.
The charger supplied was the
most powerful charger which could be connected to Ben’s small Honda
generator without overloading it and would allow the battery to be
recharged in about two hours. This charger would not need to be used
often since the battery would be mainly charged while driving from
the car alternator and kept topped up from solar panels.
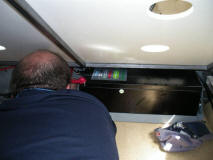
checking the
finished installation
After the battery was
installed and all of the wiring completed and tidied up it was time
to perform a few checks. The charger was connected to top up the
battery. This did not take long since when the lithium batteries are
delivered they are almost fully charged. A factory quality control
battery test report is supplied with every LiFeTech lithium battery
so it is easy to see the actual capacity and performance of each
individual battery.
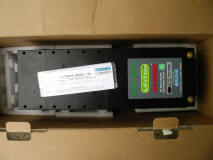
After the battery was fully
charged the battery/computer interface was tested. One end of the
data box connects to the cable which was run under the bed to the
data port on the battery. The other side of the battery data box has
two cables with USB connectors. These two connectors are plugged in
to spare USB data ports on the computer and provide power for the
data box and battery data to the computer.
After loading the battery
diagnostics software on to Ben’s computer from the supplied CD the
battery information can then be read. The battery information
available shows-
1) the voltage of each parallel cell group inside the battery
(1/1000th of a volt per cell).
2) the minimum and maximum internal recorded battery cell
temperatures
3) the ability to set upper and lower voltage alarm set points for
OHV (over high volts) and OLV (over low volts). This function is for
advanced users and allows the battery to provide output signals
which are used in more specialised applications (for example using
the low voltage alarm point signal being used to disconnect a main
power relay or contactor automatically so as to prevent over
discharge to the battery or using this signal to start a generator
automatically for charging as is often used when these batteries are
used in large boats).
The great advantage of this remote system of battery monitoring is
that it shows you what is actually going on inside of the battery
and that it avoids having to crawl under a bed or other difficult to
access location to reach the battery terminals with a multimeter,
therefore you can comfortably check your battery while being seated
or even from outside of the van.
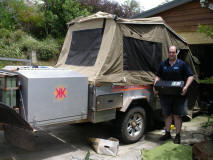
how the system works
The battery can be charged
using the same methods as you would use to charge a traditional lead
acid/AGM battery ie, alternator (while driving), mains 240V charger
and solar panels. In each case a dedicated lithium charger should be
used so as to charge the battery properly and so not void the
manufacturer’s battery warranty which can result from using a non
specific or lead acid charger which may feature modes of charging
such as “desulphation”. These “pulsing” modes are not required for a
lithium battery and must not be used. Some existing solar regulator
chargers can be reprogrammed to suit the charging requirements of a
lithium battery so often there is no need to purchase a new lithium
solar battery charger/regulator since the existing charger may be
able to be used with some slight programming changes.
Due to vastly superior
discharge curve of the lithium battery compared with lead acid
batteries it is almost essential to fit a suitable battery monitor.
This allows the camper owner to always know the state of charge of
his batteries. In addition the output relay alarm contact available
at the battery monitor can be set to provide an alarm at any
convenient level of discharge. In most battery installations this is
usually set at between 60% and 90% depth of discharge. When the
battery reaches this alarm point either a flashing warning light or
audible buzzer can be triggered drawing attention of the van owner
to recharge his battery. At this low battery capacity level, a
low voltage battery disconnect can also be incorporated to
automatically turn the battery off so it can not be discharged any
further until action is taken to recharge it.
The LiFeTech XPS and HPS
series of factory lithium batteries are unique in that they are the
only lithium battery available which can have a low voltage cut off
disconnect board fitted inside the battery and which is used in
conjunction with the BMS. The cut off board is an optional extra
which is not fitted to the standard batteries and which must be
specified when ordering these batteries. This cut off board
automatically disconnects the 12V power from the positive battery
terminal in the event of the battery being discharged 100%. In a
battery where the disconnect has activated there will be no output
voltage at the battery terminals and by checking the voltage with a
multimeter would show a reading of close to zero volts being
measured at the battery terminals. This low voltage cut off is self
resetting.
So with most lithium battery installations in campervans, caravans,
motor homes and other RV’s it is usually recommended to use both a
battery monitor or external low voltage battery disconnect as well
as the internal battery low voltage cut off board. This provides two
levels of protection and we like to think of this a bit like having
a “main parachute” and a “reserve chute”. The main parachute (or
battery monitor) is used routinely everyday to display the battery
state of charge, run time remaining, volts, amps, watts and other
information. If this device should fail (highly unlikely) the
secondary available level of battery protection (used preferably
never or rarely as in the case with a reserve parachute) is the
battery cut off board built into the battery. This acts as a last
line of protection ensuring the battery does not become discharged
below 100% state of charge and thus potentially causing serious
damage to battery cells.
While there are several
suitable battery monitors available that can be used, in Ben’s
Kimberley Kamper installation we used a Victron BMV-600S battery
monitor. There is a user review of this device here
http://www.campertrailers.org/victron_bmv-600s.htm
why would
you install a lithium battery?
Ben and many other owners of camper trailers and caravans take great
pride in their units and want to have the best systems available and
this includes batteries. Some of the reasons given by owners for
upgrading to lithium batteries include the following-
Much lighter weight The six lead acid batteries originally
fitted to Ben’s Kimberly weigh approx. 70kg in total. The
replacement LiFeTech lithium battery weighs 30kg. Not only does the
lithium battery weigh less than half the original battery weight it
also takes up close to half of the space occupied by the old lead
acid batteries. Lithium battery weight is typically half to one
third of an equivalent run time/capacity lead acid battery bank.
This is often of major importance to many owners and has been of
particular concern expressed to me by several camper trailer owners
where the batteries are installed in the front of a camper or
caravan. These owners often provide a major reason for looking at
using lithium batteries to “reduce the weight over the tow ball”.
The reduction of weight can also have a long term saving in less
wear and tear of mechanical components such as wheel bearings etc
and there may also be long term cost savings in other areas such as
with better driving manoeuvring and slight petrol savings from
towing a lighter weight camper.
Much higher electrical efficiency LiFePO4 lithium batteries
have a much higher electrical efficiency compared with lead acid
batteries. While lead acid batteries are typically 70% - 85% charge
efficient LiFeTech lithium batteries are approx 98% charge
efficient.
So what does this higher
efficiency mean in real terms? It means that the lithium battery
will charge better/faster than a lead acid battery and this can be
particularly important where only limited charging methods are
available such as from solar panels. We often receive feedback and
comments from camper owners who have upgraded to more efficient
lithium batteries and one recent comment received (which is quite
typical of feedback received) is- “previously my old lead acid
batteries would be fully charged from my solar panels by 4pm-5pm in
the afternoon but now with the new more efficient electrical set up
using the same solar panels, our lithium batteries are now fully
charged by 10am-11am”.
Since the efficiency of the
lithium batteries is close to 100%, virtually all of the power
generated by the solar panels is stored in the lithium batteries for
later use. The same cannot be said for lead acid batteries due to
gassing/recombination, side reactions and other factors due to the
very old technology of lead acid batteries and which don’t affect
lithium batteries.
Much longer working/cycle life While the initial cost of good
quality lithium batteries such as LiFeTech batteries is far more
expensive to purchase and set up initially, the actual cost of
ownership is considerably cheaper than lead acid batteries
(calculated in terms of dollars per charge cycle).
In addition is the flat
lithium battery discharge curve (the lithium battery voltage
essentially does not drop under load until the battery is almost
depleted) which allows for electrical equipment such as inverters to
run more efficiently since they are seeing a constant voltage
delivered to them (unlike with a lead acid battery where the voltage
will drop and continue to drop from the moment it is connected to
the output load devices so the connected electrical device must
always try to compensate for this continually dropping voltage until
it shuts down at its minimum operating voltage).
This means that electronic
equipment being powered by lithium batteries will usually have a
longer working life before failure than the same device connected to
lead acid batteries (known as MTBF- mean time between failure).
One other important factor
is that LiFePO4 batteries are not affected by Peukert’s Law (so in
the case of Ben’s new lithium battery having a capacity of 180Ah
while the total of the old lead acid batteries being 6x35Ah = 210Ah
the slightly smaller capacity of the new lithium battery in actual
use provides at least equal or better run time compared with the old
lead batteries).
Faster recharge Lithium batteries can be recharged much
faster than lead acid batteries. In fact the X2EF cell used in the
battery pack fitted to Ben’s Kimberley Kamper van has the ability to
be fast charged to greater than 90% capacity in 15 minutes. In
reality a fast charger is chosen to provide charging times of 1-2
hours or the charger is selected so as to not overload a typical
Honda or similar small camping generator
Other considerations Due to the higher electrical efficiency
of lithium batteries they should never gas in normal use. They can
be mounted in any orientation and can be fitted in a totally water
proof battery box since no venting of batteries is needed. This
makes it possible to drive through deep river crossings where the
batteries can be totally submerged due to the cable entries from the
battery box being made through waterproof cable glands.
LiFePO4 batteries are also
the safest battery to use and the most eco-friendly battery since
even if a battery should be damaged there is no corrosive sulphuric
acid contained in the battery which can leak out nor does the
lithium battery contain any toxic heavy metals such as lead or
cadmium.
So as Ben and many others have found, the best batteries money can
buy are available for private use by owners of camper trailers,
caravans and other RV’s and are not only available for use by
government.
For more information
regarding any aspects of a lithium battery set up in a camper
trailer please do not hesitate in either emailing or giving Armin a
call at any time for personal advice
Armin Pauza
General Manager & Principal Electrical Engineer
Lithium Batteries Australia & Aide Solar Australia
www.lifetechlithium.com
info@lifetechlithium.com
phone 0420 948 757
march 2012
|